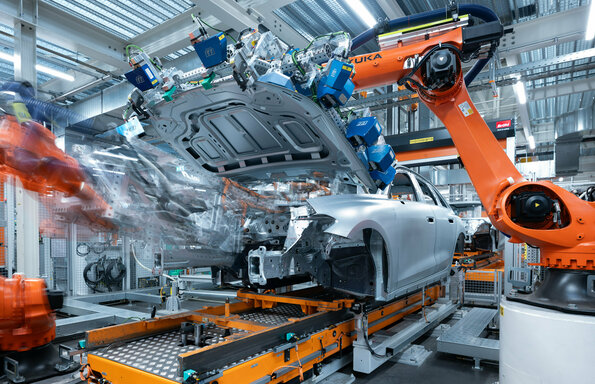
アウディが、次世代の生産ラインづくりを進めるネッカーズルム工場での最新生産ラインを公開。新たな塗装工程などで車両生産時のエネルギー消費量の削減や持続可能な水利用を実現したという。同社が電動化戦略とともに推し進める「360ファクトリー」と呼ぶ生産改革に沿ったもので、「新型アウディA5」で初採用される次世代プラットフォーム「PPC(プレミアム・プラットフォーム・コンバッション)」によりネッカーズルム工場でも電気自動車(BEV)の最新鋭の生産体制を実現することになる。
ネッカーズルム工場で2025年以後にカーボンニュートラル化
アウディは2025年以降、ネッカーズルム工場で生産されるすべてのモデルをカーボンニュートラルにする方針だ。このため、より効率的な生産ライン、より高度な自動化、そして革新的な技術を積極的に導入していく考えで、なかでも新たな塗装ラインは「自動車業界で最も近代的なもののひとつとなる」という。今回、同工場で「新型アウディA5」の生産開始に合わせて、同工場で取り組む革新的な生産体制を公開した。
同社生産担当のゲルド・ウォーカー取締役は「長年にわたる内燃エンジン車の生産経験と、複雑な立ち上げに関する専門知識により、ネッカーズルムのチームは理想的な前提条件を備えている」と話し、ネッカーズルム工場のフレッド・シュルツ工場長は「将来に備えた生産工場インフラを構築した」という。2025年までに、ネッカーズルム工場は世界中のアウディの拠点と同様に、カーボンニュートラル生産を実現する計画だ。
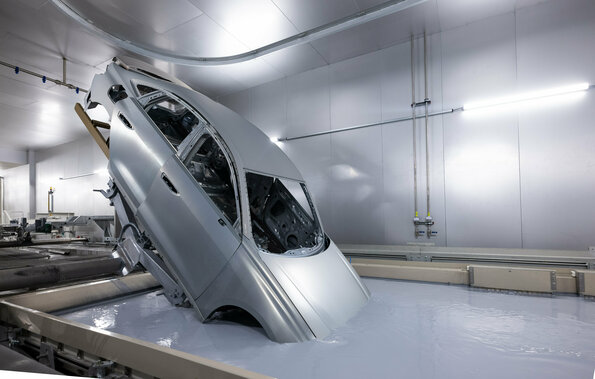
塗装工場を改修しエネルギー消費を大幅に削減
その代表的な取り組みが、2025年に完成予定の塗装ライン。同社は「自動車業界でも最も近代的な工場のひとつとなるだろう」というもので、新型アウディA5の発売に向けて環境に配慮した工程を導入している。同社はすでに、水性塗料を使用しているが、この最新モデルでは新たな塗装工程として下塗りのフィラーは追いがけ塗りとなるウェット・オン・ウェットに置き換えた。これにより、フィラーの個別乾燥は必要なくなり、塗装工程におけるエネルギー消費を1台あたり最大140kWhと大幅に削減することが可能になったという。
また、カソード浸漬塗装では車体をタンクに逆さまにして浸漬し回転させることで、気泡や汚れの付着を最小限に抑えた。これにより、省スペースで徹底した処理が可能にしたほか、カソード浸漬塗装の乾燥で従来の外部乾燥プロセスに代わって、いわゆる横方向乾燥プロセスを採用、内部に空気を吹き込み、車体を内側から加熱することで高いエネルギー効率を示し、将来のBEVやハイブリッド車の強化されたフロア構造にも適応するという。これらにより、同社は車両あたり約50kWhのさらなる省エネを実現。また、これまで100%新鮮な空気を含む水で回収され、廃棄していた塗装ミストを新しい乾燥分離プロセスでは、最先端のフィルターで捕集し、フィルターを通過した空気の90%以上を再利用することが可能となった。従来のウェット分離とは異なり、真水や化学薬品の使用も不要になったとしている。
生産における持続可能な水の利用
アウディは2035年までに、生産における環境負荷の高い水の消費量を半減させることを目指している。このため、ネッカーズルムでは工場に隣接するウンタース・ズルムタール廃水処理施設を利用したクローズド・ウォーター・サイクルを採用している。近隣のネッカー運河から処理水を汲み上げる必要がなくなり、2025年以降は淡水の使用量を最大70%削減することができるとしている。
資材の80%以上を自動搬入
さらに、ネッカーズルム工場ではグループ内で初めて、ボディショップのすべての追加部品を完全に自動で取り付ける設備を導入した。これにより、取り付け精度を向上させた。複雑な作業が必要となるフェンダー取り付け作業でも、7台のロボットを同時使用している。アウディの「360ファクトリー」戦略では、サプライチェーンもスマートで自動化された材料供給を図る計画だ。各拠点ごとに自動化ロードマップを作し、実現に向け取り組んでいる。 ネッカーズルム工場でも2014年に、場内を自由に走行する無人搬送システム(DTS)を稼働させており、今回の「新型アウディA5」の生産開始でボディショップで使用する資材の80%以上を自動的に供給されるようになった。
車体製造では世界初の試みとなる、実質的に煙の出ないはんだ付けも新たな挑戦のひとつだ。例えば、ドアなどの接着された部品を内側と外側の部品が滑らないようにはんだ付けするが、これまでは煙が腐食性であるため多くのはんだ付けポイントを清掃する必要があった。新しいプロセスでは、回転するガス流で残留物の蓄積を解消させ、以前と比べて倍以上の速さで作業を行うことができるようになったという。
ボディショップにおける最先端の品質モニタリング
ボディショップにおける品質管理測定も改革のひとつだ。車両を生産ラインから取り外すことなく行えるのがポイントだ。2つのステーションに各4台のロボットを配置、測定センサーを使用して部品の寸法精度を測定する。測定結果をすぐさま評価し、従業員が視認できるようにした。この新技術で生産されるすべての車両をライン上で直接測定することができ、同社は測定回数を大幅に増やし、いかなる偏差にもより迅速に対応できるようになった。
加えて、従業員は拡張現実(AR)などの革新的な技術を車体の検査に活用。市販のタブレットに搭載されたカメラ付きARアプリで、リアルタイムで確認すべき接続ポイントが表示され、例えば溶接の継ぎ目やポイントが目標仕様通りに存在し、実行されているかどうかを検査し、直接記録することが可能になった。(2024年8月14日)*8月12日にアウディが公開した資料を意訳した。